All Articles Written by K.J. Zeoli. Copyrights Apply
Both the Harley Davidson & Indian project are for sale
The Harley is a racer with original factory racing frame and original factory racing motor $20,000 Canadian Dolars
Our 1920 Harley Davidson JD Board-track Racer Restoration Project

Brazing a cast iron exhaust housing for the 1920 Harley Davidson Board track racer
Identify the alloy
Cast irons are essentially iron-carbon alloys. Grey cast iron has a high carbon content that is typically 2–4%. The high carbon content gives the cast iron its quality of hardness. However, the high carbon content which gives cast iron hardness quality comes at the expense of ductility. Cast iron is less malleable in comparison to steel or wrought iron.
The heating and cooling cycles during the welding process causes the cast to expand and contract inducing tensile stress. Cast irons do not stretch or deform when heated or stressed, instead, they crack, making them extremely difficult to weld. This characteristic can be improved by adding different alloys.
Grey cast iron is the most common form of cast iron. During the manufacturing process, some carbon turns into graphite flakes, which causes a pearlite or ferrite crystalline microstructure. The graphite flakes in grey cast iron may enter the weld pool causing the welded metal to become brittle.
All castings should be properly prepared prior to welding. All surface materials should be removed to completely clean the casting in the area of the weld. It is best to apply heat carefully and slowly to the weld area for a short time to remove entrapped gas from the weld zone of the base metal.
A test for checking the readiness of the cast iron surface is to put down a weld pass on the metal, it will be porous if any impurities are present. This can be ground off, and the procedure repeated a few times until the porosity disappears.
All cast irons are susceptible to cracking under stress. Heat control is the single most important factor in avoiding cracks. Cast iron welding requires a pre hearting coupled with low heat input and slow cooling. Heat control reduces thermal expansion. When metal warms, it expands. No stress is caused when an entire object warms and expands at the same rate, but stress will build when heat is localized in a small heat-affected zone (HZ).
Localized heating causes expansion within the heat affected zone and is contained by the cooler metal around it. The degree of stress that localized heating places on the metal depends on the thermal gradient between the heat affected zone and the casting body. With steel and other ductile metals, stress built by restricted expansion and contraction is relieved by stretching. Unfortunately, the low ductile characteristics of cast iron do not allow for stretching. Pre-heating decreases the thermal gradient between the casting body and the heat affected zone minimizing the tensile stress caused by welding.
The cooling rate of cast iron is an additional issue that has a direct impact on the stresses produced at the weld. If the cast iron cooled too rapidly contraction occurs, which creates brittle, easily cracked welds. Natural cooling reduces hardening and contraction stress
Best Practices for Repairing Cast Iron Motorcycle Barrel Fins
If you don’t happen to have a metallurgy lab at your fingertips it can be a very hard and daunting task to determining the type of metal you have on your hands. For welding cast iron barrels on any vintage motorcycle you can try the following steps to determine the carbon content, type of steel etc.
A simple way to start to identify your metal is to use the spark test, which is easily done with a small hand grinder on an innocuous piece of the metal.
(See the below chart for details on the grind test)
Grind or Spark Test Chart

TIG welded cast iron 1920 Harley Davidson barrel fins
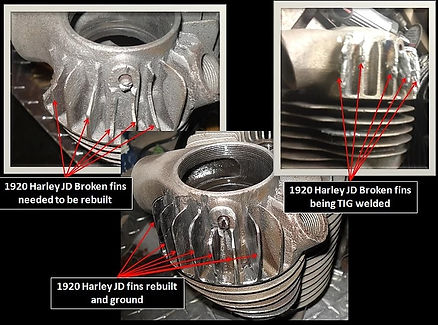
The use of a cell phone to capture a picture of the sparks, makes it easy to then compare them to the spark chart.
With cast iron you can also perform a "puddle test". Chose an un-invasive spot where it will not compromise the part. Before performing the puddle test, utilize a file to determine how the metal cuts before vs. after the puddle test.
When producing the puddle, even if only for a microsecond, you know the metal has reached its melting temperature, and also any phase transformation temperature. As the metal cools quickly, the surrounding cooler material within the puddle area simulates an annealing process. If the metal has more than 3% carbon, it will harden, if the metal has a full 2 or 3% carbon, like cast iron, it will have the characteristics of being very brittle, similar to a piece of glass. A file can then be used to determine if the surface can be scratched. If the surface cannot be scratched with a file then you know you have cast iron.
A nickel or low carbon steel filler rod is best suited for tig welding cast iron. The jugs must be preheated prior to tig welding. Without preheating the barrels, carbon may concentrate in the weld zone and the weld will shrink to rapid, this can also cause Toe or under-beads cracks. Best practice is to peen the weld once the metal is pre-heated, (Peening is used to facilitate a weld joint to stretch as it cool, thus relieving internal stresses. Peening is done by lightly tapping the metal with the rounded end of a ball peen hammer. Consideration should be taken that an excessive amount of hammering can add stresses to the weld or cause the weld to work-harden and become brittle.
Peeing cannot be accomplished In the case of repairing the barrel fins due to their nature. One other option in repairing the fins is to braze them with a cast iron filler rod, as mentioned in the above information. If using cast iron rod filler rods to repair the fins the metal must also be preheated as with tig welding.
Ultimately, getting the weld to fuse to the cast, post-heat (glowing red hot), allows the carbon concentrated along the edges of the weld to spread back out into the surrounding metal. A combination of preheating the metal along with post-heat treating and slow cooling, will even out the contraction of the weld with the surrounding metal reducing stress cracks.
The Birth of the F-Head Engine "Harley Davidson Style"
Harley’s original motor was the single cylinder 440cc IOE or Inlet over Exhaust, F-Head engine. The engine was truly an advanced piece of machinery for the day. The inlet valve was placed at the top of the cylinder head, and was opened by a vacuum force which the piston supplied on its down stroke. Also located at the top of the cylinder was the spark plug.
Going to a V-twin design was the next step for Harley, as the additional cylinder added more power and offered a better balanced motor. Indian was having great success with their V-twin introduced in 1905, which lead to Harley designing their own V-twin power plant. In 1911, Harley-Davidson introduced their enhanced V-twin. The updated motor saw the elimination of the atmospheric inlet valves, by replacing them with intake valves that were mechanically opened using external pushrods.
The valve design remained an F-head, but the addition of the pushrods meant that the motor could rev higher and create more power. The 50 cubic inch motor produced 11 horsepower. Other changes saw the magneto moved from the front of the motor to the rear, reversing the oval shaped timing gear case cover giving the motor a more distinctive look.
F-Head cylinders were cast as one piece, as opposed to other motorcycle engine manufacturers of the day who employed a separate barrel and head configuration, similar to today’s motorcycles. The reason Harley Davidson chose to cast the F-head cylinders as one piece, was due to the lack of materials that were available for cylinder head packing at the time. Obtaining a gas tight fit between the cylinders and heads was hard to achieve. The two main materials used for seals were sheet asbestos, which often failed to provide a sufficient amount of strength to resist the high cylinder pressures, and copper sheet metal gaskets were too hard to conform to the many irregularities in the castings.
The cylinders are comprised of close grain grey iron, which contains considerably more phosphorus than is usually found in other grades of cast iron. Manufactures of the time used high a phosphorus count in the metal, which allowed the molten cast iron to flow into all the small cracks and crevices that make up the cylinder. Tungsten was also added to the metal as it added a high degree of heat resistance to the cylinders.
A one piece cylinder offers an advantage as it eliminates any leaking between the head and cylinder as in a two part unit. There are more detractors with the one piece cylinder as the piston cannot be accessed for heavy carbon removal. A one piece cylinder unit also complicates things when boring and honing must be done on the cylinder walls.
The cylinder must be blind bored as the head is not detachable. WHAT IS A BLIND HOLE? A hole or a bore having a bottom, a shoulder, or any surface obstruction which would prevent a tool from going all the way through, is termed a blind hole. To complicate the boring process even more, the Harley Davidson J model cylinders have a slight tapper.
The basic principle of precision honing is that to achieve a straight bore the honing tool must be straight in a blind hole this means the honing tool shoe and stone must be straight, clear down flush to its front bottoming end. Not only must the stone and the shoe be kept straight but they also must match the work radius to maintain stability.
The F-head motor was constructed with the intake valve at the top of the combustion chamber. Placing the intake valve on the top of the cylinder does have its advantages, as the intake piston is proportional large and its location allows for an efficient distribution of the air/fuel mixture. The spark plugs location also offers an efficient way to ignite the air/fuel mixture. Placing the valves at the top of the motor also allows for direct inflow, while creating minimum back pressure during the exhaust stage.
